Case Study
Hanwha Total Energies
Reducing Travel with Assisted Reality
Challenges – Uninterrupted maintenance when travel is not an option.
Petrochemical plants have many sophisticated processes and machinery. Hanwha Total operates one of these complexes that produce various products in a vertically integrated facility. With so many moving parts working together, it is vital to keep inspections working around the clock. With over 80% of the devices being overseas sourced, the plant receives international engineers regularly to provide support. But when COVID-19 disputed all international air travel, the visits also had to stop. Hanwha Total sought a way to overcome the pandemic and keep maintenance uninterrupted.
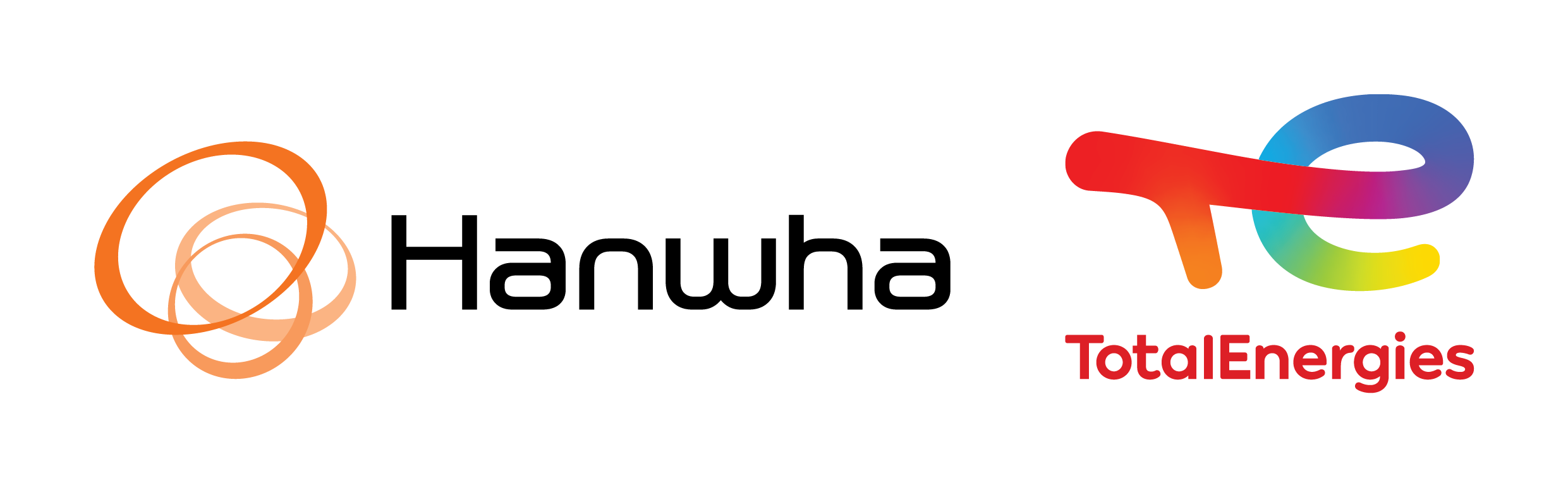
Hanwha Total – A Vertically Integrated and Diversified Manufacturer, Where Safety is First.
Hanwha Total Petrochemical Plant is a subsidiary of Hanwha Group, a leading conglomerate in South Korea.
Hanwha is the market leader in critical inputs for producing solar cells, automotive parts, and electronics and produces all sorts of materials ranging from ethylene glycol to jet fuel to EVA.
The petrochemical plant in Korea operates globally, continuously communicating with engineers located in various countries such as France, Germany, and Japan.
Introduction
Hanwha Total Petrochemical Plant regularly maintains their facilities, involving supervisors from overseas-manufactured equipment. With over 80% of parts coming from abroad, the travel restrictions imposed after COVID-19 suddenly created a significant challenge for coordinating maintenance.
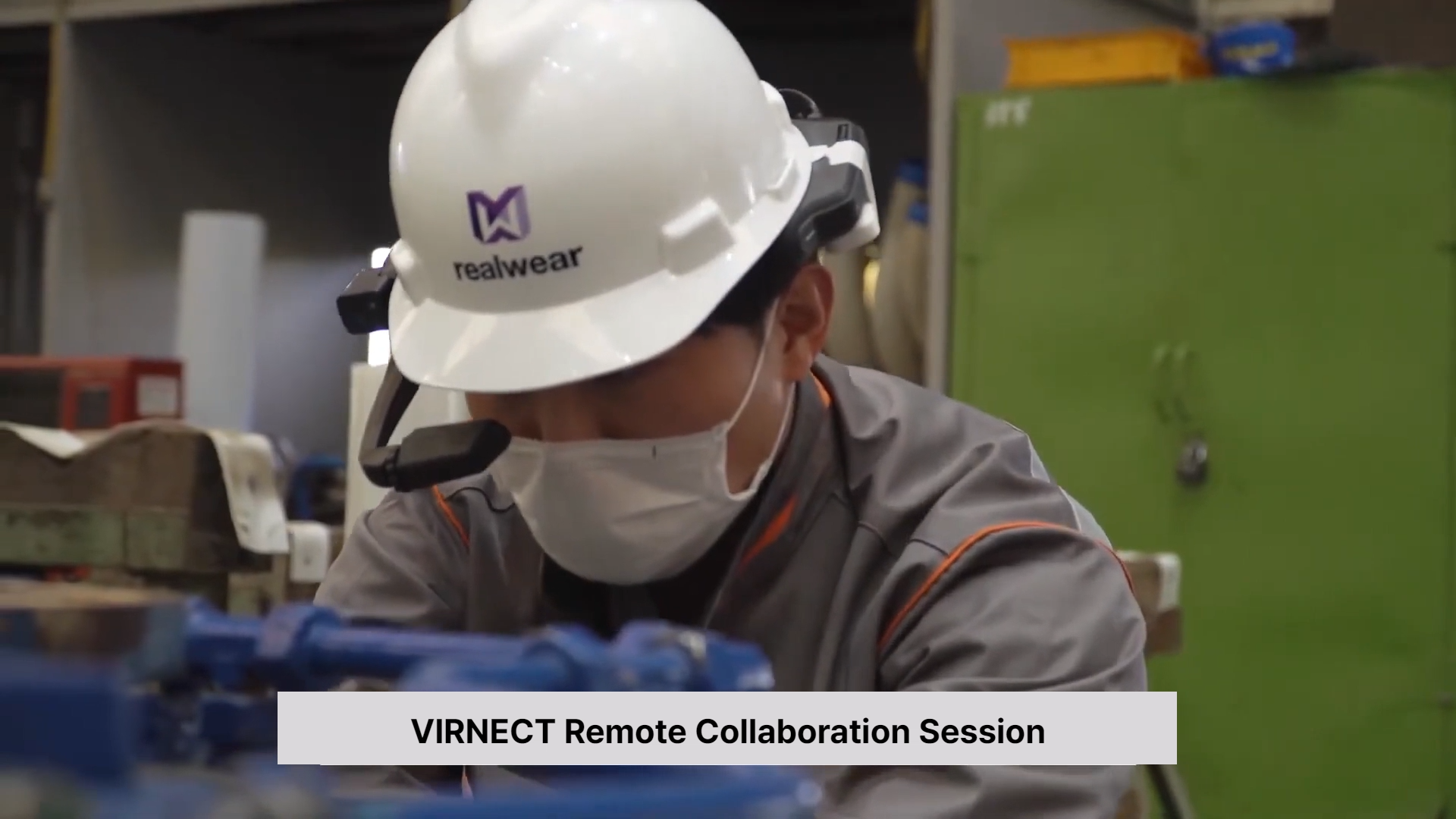
Working hand in hand, from anywhere.
To solve this challenge, Hanwha Plant introduced a VIRNECT remote. The software allows field workers, local supervisors, and international experts to collaborate seamlessly.
Workers connect via a smart glasses collaboration system that allows maintenance engineers in Korea and experts from overseas equipment manufacturing companies to work from a distance.
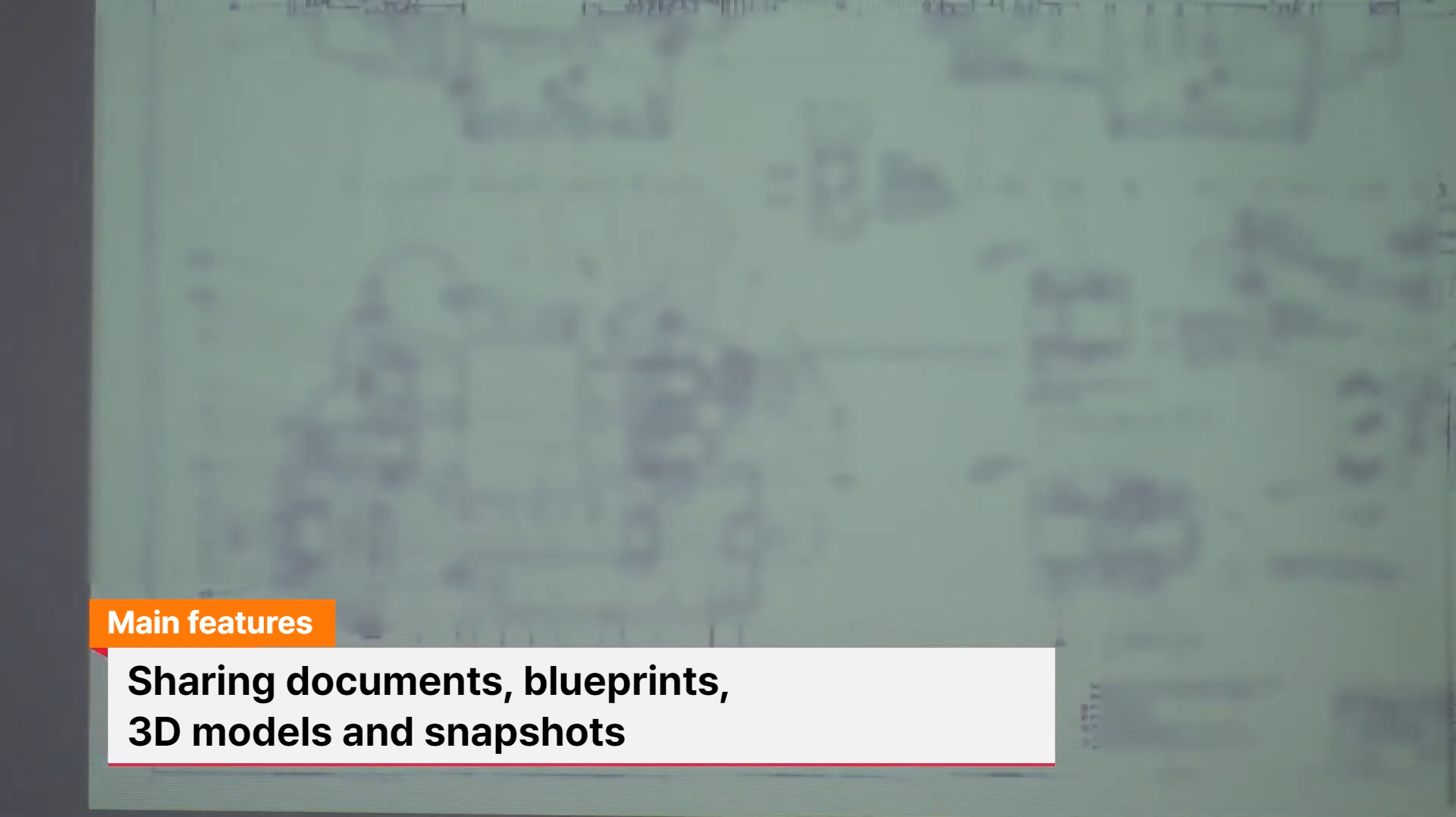
Smart glasses were also introduced to make communication easier, freeing up hands to move around the site or work. The remote collaboration system can be used on mobile devices or PCs.
The system relies not only on verbal communication; it also allows parties to refer to physical elements and share reference material. Pointing both at the screen and at blueprints or documents facilitates communication.
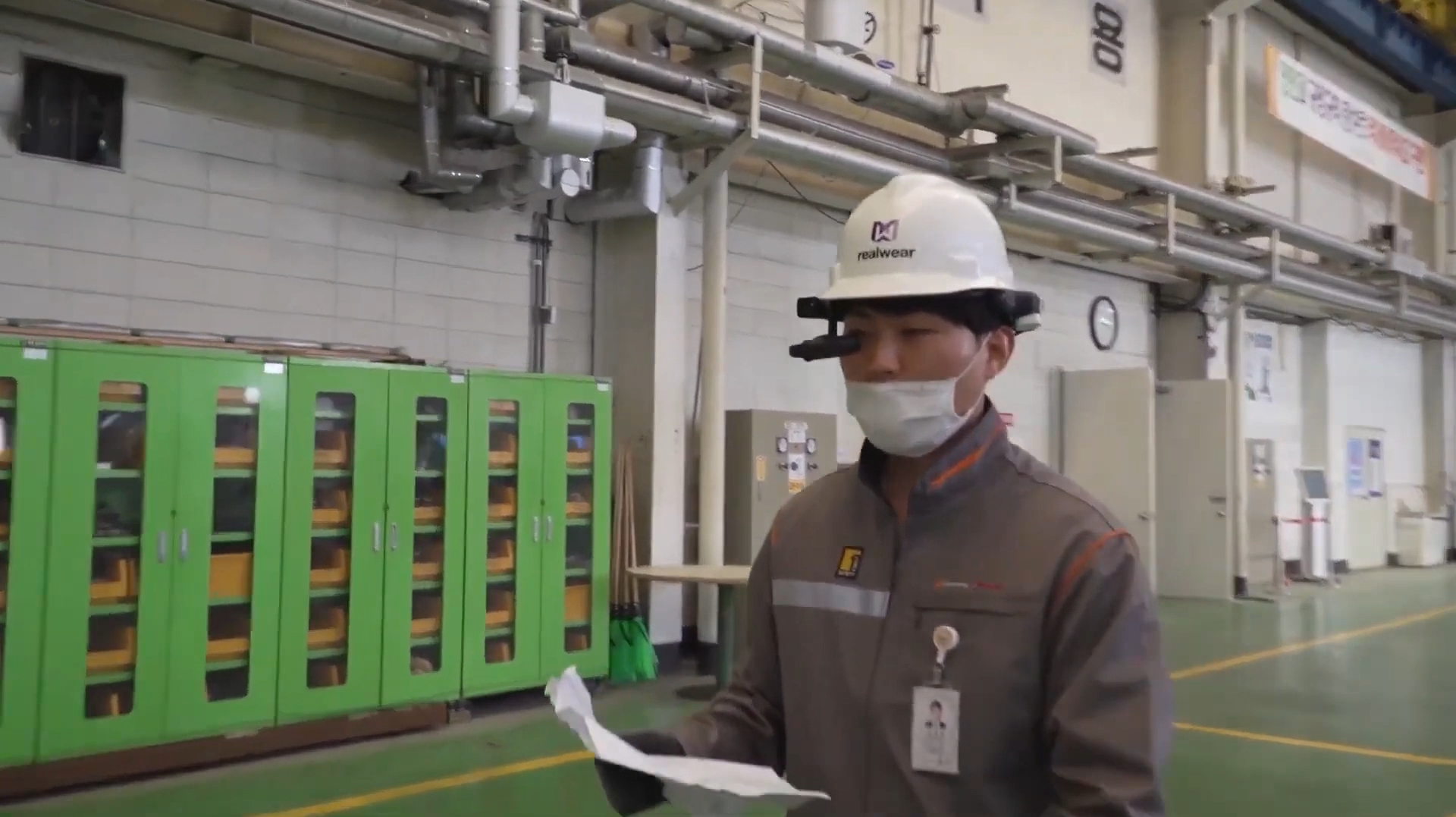
A Challenge Turns into an Opportunity.
What started as a way to overcome COVID regulations became a strength.
With the introduction of the remote collaboration system, screens were shared with engineers located in various overseas countries, allowing maintenance to be performed even if production experts were not present. The use of smart glass equipment also increased the use of remote collaboration as there was no need to hold the device for collaboration with the hands.
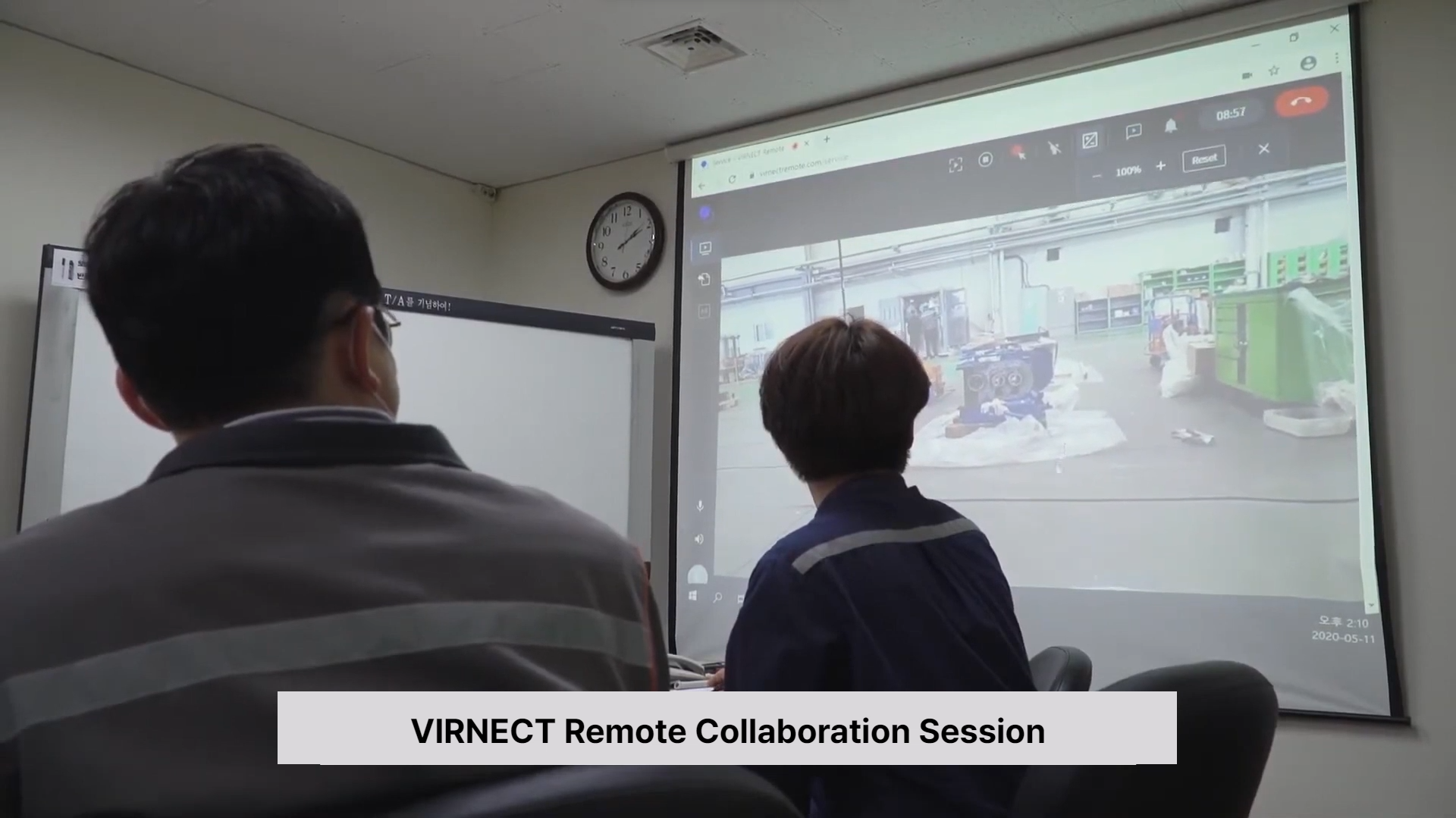
Hanwha Total Petrochemical Plant saved about 90% of technical support costs by significantly reducing the time and cost required for overseas business trips.