Extended Reality:
The Future Of Manufacturing
With Extended Reality, you can decrease downtime, troubleshoot remotely, increase your resilience, and add top line growth.
Stay relevant, innovative, and competitive with XR.
In an XR rich environment, experts can provide remote assistance, work instructions, or training modules at any time. You can streamline knowledge-intensive workflows, boost productivity, enhance business processes, and provide an exceptional customer experience.
XR in manufacturing is inevitable: elevate your operations and gain a competitive advantage.
XR is a collaborative solution to decrease your downtime, improve your operational efficiency, and expedite your repairs. XR users in manufacturing see improved resiliency and decreased downtime: culminating in an operations and productivity transformation.
With XR, you can decrease downtime and streamline operations.
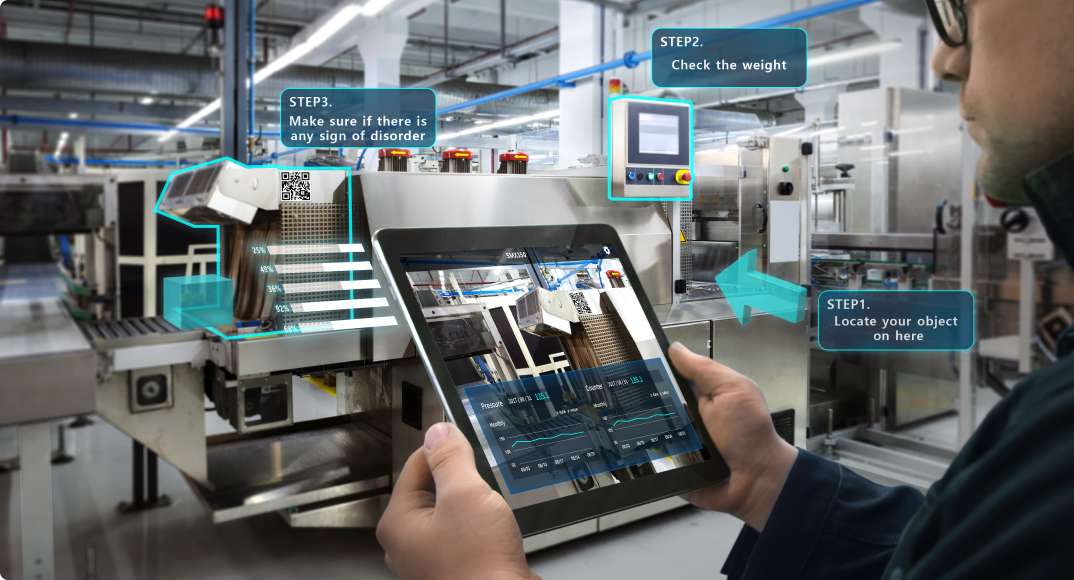
Build Digital Twin Models
Our platform, Twin, allows you to build an exact replica of your facility, equipment, or process. You can model scenarios, test, and forecast from the comfort of your computer with this digital twin.
Remotely Maintain Equipment
XR allows you to remotely check-in on your equipment, machine health indicators, and operational metrics in real-time. With your metrics readily available, issues can be caught early and quickly dealt with. You can also relieve stress and pressure on those who are on-site, improving employee morale.
Remotely Inspect Facilities
No matter where you are in the world, XR offers the ability to remotely inspect facilities. You can monitor as if you were standing on-site yourself. As issues arise, you can assist and troubleshoot in real time.
Collaborate With Experts Anywhere
XR is the ultimate in collaboration tools. It goes further than talking to people: it allows experts from all over the world to brainstorm and collaborate as if you were standing in the facility together. This is a powerful virtual experience that can expedite repairs and improve first-time fix rates.
Recruit Top Talent
With the rise of remote work, highly qualified people want to work for innovative companies from anywhere in the world. By opening up the doors with XR, you will be able to work with talent from all over the world! You no longer need to find someone willing to move and pay their moving expenses. They can work from the comfort of their home office.
Improve Employee Retention
Employees are looking for companies who are innovative and care about their well-being. With our XR technology, we have seen a reduction in workspace accidents and, in turn, an improvement in employee retention. With improved learning and development opportunities, companies are able to recruit and maintain a younger workforce.
Improve Information Accessibility
VIRNECT’s XR platforms are designed to be highly accessible: viewable on any number of tablets, phones, and computers. Our platforms are also compatible with equipment you already own, such as drones and robots.
Decrease Downtime
We know speed is of the utmost importance when it comes to fixing down equipment. With the ability to remotely inspect on-site tools and equipment, your team of experts can fix problems as they arise without putting a specialized technician on location.
Decrease Learning
& Developing Costs
With XR technology, training is simplified! As a technician views equipment while wearing Smart Glasses, they will see an overlay of 3D models, exploded view diagrams, step by step instructions, and more. This not only improves employee retention, it expedites training: saving you time and, in turn, money.
Reduce Errors
One of the most powerful aspects of XR is being able to see instructions as you need to complete them. Using hardware, like Smart Glasses, technicians and on-site laborers can see detailed overlays explaining exactly what needs to be done. This frees up both hands to work and improves accuracy.
Discover a new way to interact with the world around you.
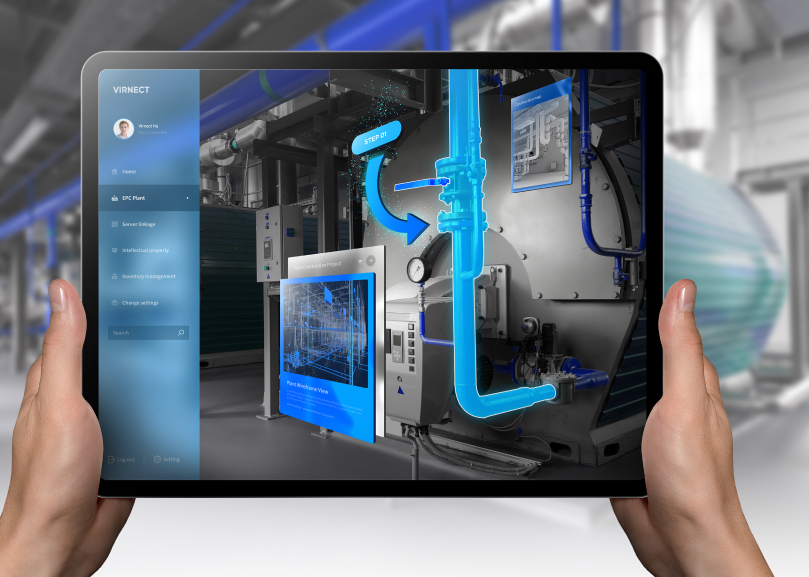
Our suite of AR platforms offer a variety of powerful solutions, designed to decrease downtime and yield loss, improve your bottom line, and empower your workforce. We currently offer 4 platforms (Remote, Make, View, and Twin), each offers unique value to a manufacturing organization.
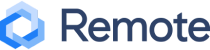
Remote brings international teams together for fast fixes.
VIRNECT’s Remote uses XR technology, like Smart Glasses, to decrease your training costs, time, and workplace accidents. With the glasses, your employees will be able to see a smart overlay on top of what they are looking at, such as complex machinery. Remote is the XR platform that mitigates risk by freeing up your employees’ hands and making paper manuals and PDFs obsolete.
But that’s just the tip of the iceberg. Remote connects people all over the world for maximum collaboration! Using any device with a camera, you will be able to see exactly what your on-site workers are looking at. You’ll be able to troubleshoot problems with equipment and provide assistance, minimizing downtime and improving resiliency. With more eyes on the problem, you can also improve your first-time fix rate.
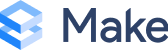
Make allows you to create no-code, interactive, and intuitive XR content.
VIRNECT’s Make is a premier XR content creation tool that anyone can use. By simply dragging and dropping different elements into place, you can create comprehensive walk-throughs and explanations for anyone in the world.
Using Make, you can create company, process, and equipment specific XR content. Employees on-site can use the guides to replace manuals and PDFs. No matter how customized or specialized your equipment is, Make allows you the freedom and flexibility to train your employees quickly, replace manuals effectively, and conduct maintenance easily.
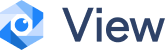
View brings XR content to technology you already have.
VIRNECT’s View allows you to access AR content on a wide array of platforms. It is an excellent continuation of Make, as it allows you to access that XR content on computers, tablets, phones, and more. Moreover, View also allows for visual overlays.
For example, you can hold a tablet up to a piece of equipment and see your XR content on how to maintain, fix, or operate that piece of equipment.
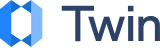
Twin creates a digital twin of your facility for powerful remote monitoring.
VIRNECT’s Twin is a powerful platform that builds an XR replica of your facility. This is an exact replica that allows you the freedom to test and build different scenarios without the typical R&D costs. Can your operation be more efficient? Are there deficits anywhere? Twin can tell you.
On top of that, Twin tracks and provides data real-time, allowing you to monitor your facilities from anywhere in the world.